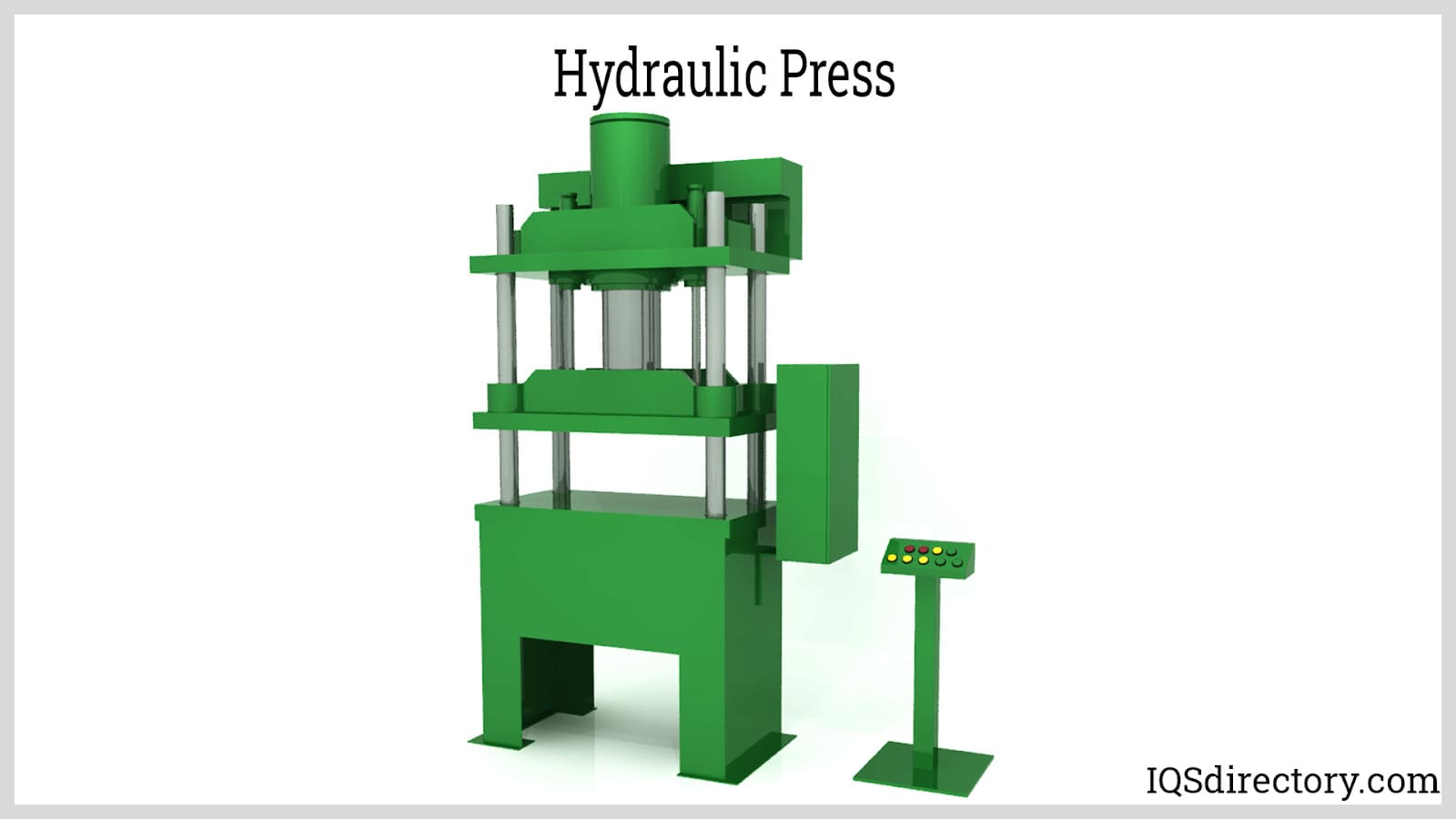
Across a wide range of industries, hydraulic presses play a key role in fabrication, assembly and maintenance, helping operators fit, bend and assemble sheet metal, parts, bearings and equipment.
What Is a Hydraulic Press?
A hydraulic press is a device used to press out materials, aiding facilities in fabrication, assembly and maintenance. It employs pressure generated by a pump to push a steel cylinder into a material at a set force.
The main parts of a press include:
- A frame that holds the press together and gives it strength, with different frame shapes used for various pressing applications
- A table or bolster, which supports the material as it is pressed and can often be repositioned to properly line up materials with the press
- A hydraulic steel cylinder or ram, which is extended to apply force to compress parts or separate them.
- A pump that uses hydraulic fluid to create pressure that drives the cylinder to create a specific force output.
Presses are used in a variety of facilities and applications where materials need to be pressed together or separated. Presses are typically used to press two things together or press two things apart, such as bearings, other shaft fitted metal parts or to bend or straighten materials. Certain smaller presses, such as C-frame presses, can also be used to hold materials together during assembly or to disassemble parts for maintenance.
How Do Presses Work?
While there are many different types of presses, each hydraulic press works in essentially the same way. Presses are powered by a hydraulic pump, which can be manual, pneumatic or electric depending on the application and press size. Pumps create a fixed pressure that determines the force of the press, rated in tons. Once engaged, the pressure created by the pump forces the pressing cylinder to extend. This cylinder makes contact with the material, pressing against it with a set force controlled by the pump.

Once pressure is removed, the cylinder retracts to its housing. The process is repeated with each press operation. In larger scale pressing operations, or when a press is frequently used, pumps may be electric- or air-operated to reduce the need for a press operator to control the pressure by hand. Operators may also set the press and the bolster one time and complete repetitive tasks without the need to constantly realign or adjust the press.
Varying the pump type that you choose to create more or less power allows press force to be controlled. The most basic pump is a hand-operated model, used for low-volume, low-force tasks such as folding metal or placing bearings. Hand pumps allow the press to move as quickly as you pump, while electric and air pumps can provide more consistent, even force. Operators set up a press before each application, so that the right force, alignment and spacing are achieved. Presses need to be adjusted when materials or parts are changed.
What Types of Presses Are There?
H-Frame
H-frame presses are large floor units that combine a steel frame, a press cylinder, a pump and a movable bolster—forming an “H” shape. These presses can be used for a variety of applications, including in repair and maintenance facilities and on production lines for assembly. H-frame presses are typically paired with hand pumps for low-volume applications, with air pumps in facilities where pressurized air is available or with electric pumps for consistent operation. Cylinder size can also vary depending on the force needed and the application.
Roll Frame
While similar to H-frame presses, roll frame presses feature a table that can be several feet long to accommodate large materials, at the bottom of the press frame. Depending on the model, either the table or the press frame can move, allowing operators to make more calculated presses when working with large or complex materials. Roll frame press operators will often use a forklift or an overhead lifting system to move materials onto the press, and slide either the frame or the table (depending on model) to align the press and materials appropriately, explains Kurt Huber, Senior Global Products Manager for Tools at Enerpac, a global manufacturing company that produces hydraulic presses. Roll frame presses allow operators to bring materials down safely and slide them into the press, rather than risk an accident with a large workpiece.
Bench Frame
Like H-frame presses, bench frame presses combine a press cylinder with a steel frame. Bench frame presses are smaller than H-frame presses, can mount to tabletops or workstations and often feature hand pumps and removable cylinders. Facilities with higher-volume applications, explains Huber, will often use bench frames to rapidly assemble bearings or other parts, saving space when compared to larger H-frame models. They can also be used for lower-volume or smaller fabrication tasks such as bending metal parts.
Arbor Press/C-Frame
Arbor presses and C-frame presses both take on a smaller, more mobile design than larger H-frame models. These presses combine a solid steel frame with a removable cylinder. The major difference between arbor and C-frame presses is that arbor frame models are designed to be mounted onto a surface and feature mounting holes. Arbor frame presses can also handle higher tonnages for more intense pressing applications. C-frame presses are designed to be more portable and can be used to hold parts in place for assembly, or can be used to remove components or mount to a bench for repetitive tasks such as bearing installation.
While hydraulic presses all work the same way, they come in a range of types and sizes based on your specific needs. Now that you know the types of hydraulic presses and how they work, you can choose the right one for your application.